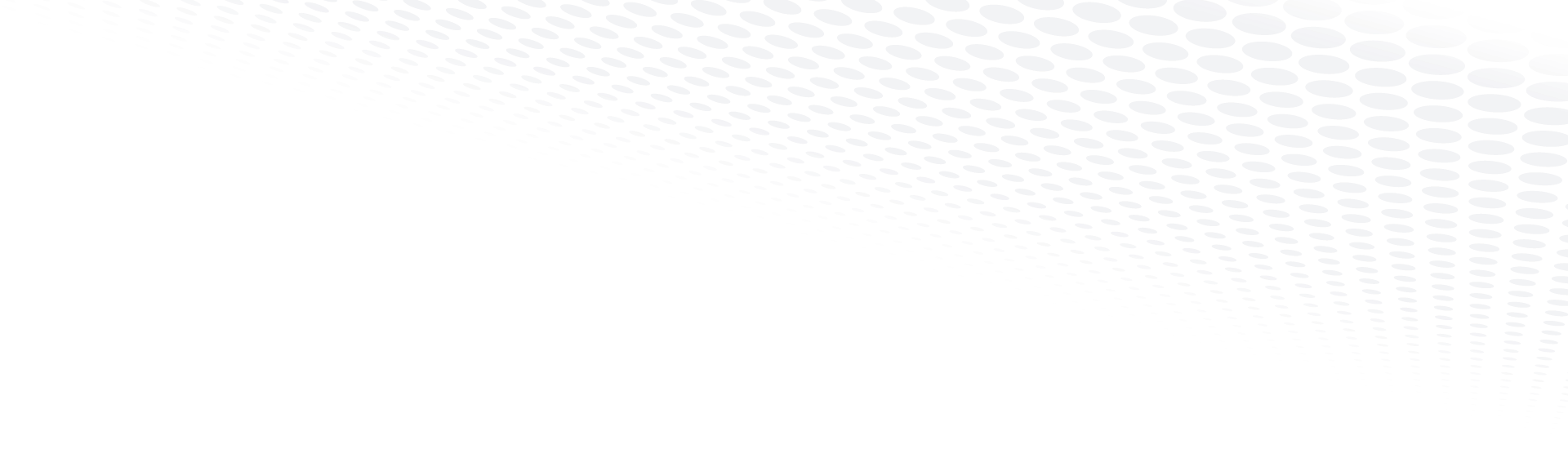
Nanosecond Fiber Lasers
IPG Nanosecond Fiber Lasers are ideal for industrial applications from laser ablation, marking, trimming, scribing, foil cutting, micro-machining, diamond and silicon cutting, to microwelding and high speed hole drilling. They feature low divergence and can provide the high power density and fluence required for high speed processing of both plastics and metals, including highly reflective materials.
High power pulsed lasers are optimized for large throughput surface treatment applications. From UV to Mid-IR, from a few Watts to multiple kW power, the versatility of IPG pulsed fiber lasers is unparalleled.